Latitude is developing a launch vehicle and engines to send small satellites into space, and HEROSE products are part of the rocket‘s fuelling process.
The countdown begins, the valves open, and the kerosene-like rocket fuel RP-1 flows into the combustion chamber along with cryogenic oxygen. The engine ignites, and combustion starts. The power of the engine is immediately felt on the test stand, and the data align as expected. Justine Gouraud, a fluid engineer at Latitude, has worked long and hard for this moment.
A new space age begins
For a long time, space exploration was the domain of countries and their space agencies. Today, young private companies are revolutionising the market. Data from small satellites, or Smallsats, are becoming essential for a variety of modern digital applications. Without a strong presence in space, future technological leadership on Earth is at risk.
Smallsat data are becoming increasingly crucial for many business models: satellites enable fast internet access worldwide, real-time Earth observation for agriculture, science, and government purposes, logistics, Industry 4.0, autonomous driving, climate monitoring, and the development of new technologies. Many of these services rely on satellite constellations, which require a large number of Smallsats in space.
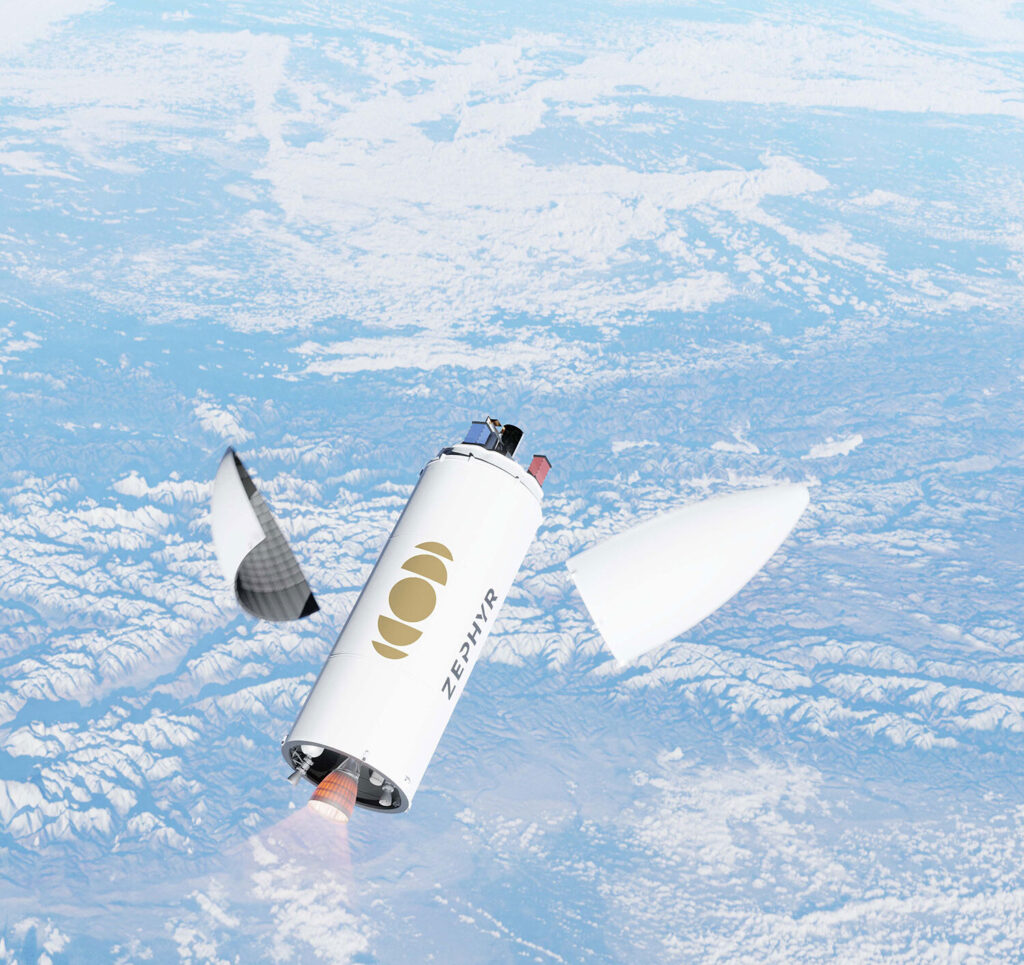
High ambitions at Latitude in France
In the NewSpace sector, which refers to the commercialisation of space, many startups aim at lowering the barriers to space entry. The French company Latitude has been around for five years and is already developing a launch vehicle and engines to execute soon a schedule of 50 launches per year. Latitude is not only developing the launch vehicle and engines but also the ground equipment necessary for engine tests and launches.
The past 15 months have been eventful for Latitude: two successful engine test programmes, significant performance improvements in the upgraded rocket engine, and the opening of a 3-hectare test centre for liquid propulsion in France. In early 2024, Latitude announced a Series B funding round of $30 million, supported by existing investors. Currently, 130 employees are working towards Latitude’s ambitious goals.
We use HEROSE products in our three test benchesand are very satisfied with their performance.
Adrien Bourasseau, Latitude Deputy Head of Test Department
Equipment for cryogenic environments
Developing and testing the Navier engines is a particular challenge. The test stand must be meticulously prepared, ensuring all fuel line connections, sensors, and controls are secure and verified. The cryogenic liquid oxygen requires special attention. This is where HEROSE products come into play, having proven their reliability thousands of times in cryogenic environments. Latitude chose to partner with HEROSE due to its extensive experience and professional consultancy. HEROSE valves, filters, and check valves are used in the cryogenic lines to supply the engines with liquid oxygen and liquid nitrogen to cool the oxygen.
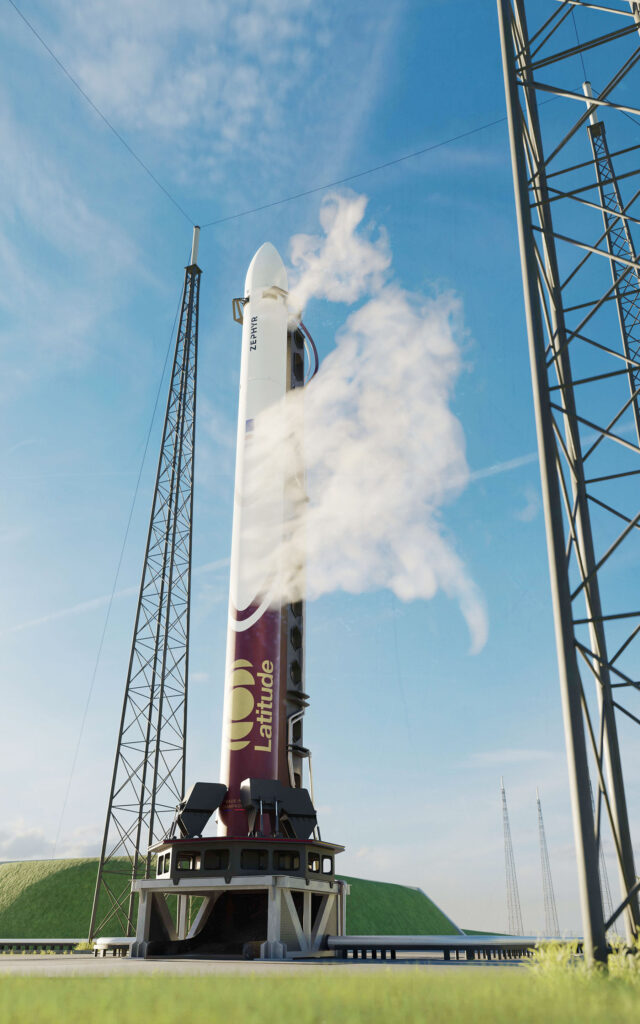
This is what the Latitude rocket will look like when it is on the launch pad for the first time in 2025.
Cutting-edge methods for rapid progress
Many rocket engines share a similar construction. Inside the engine are channels through which kerosene flows to cool the combustion chamber and improve injection. Latitude’s Navier engines are manufactured using a 3D printer. “With 3D printing, we can move much faster and implement improvements in a short time,” says Adrien Bourasseau. This technology allows for high design flexibility, enabling the testing and optimization of different channel designs. The speed of the technology is crucial when needing about 400 engines per year.
Latitude has named its launch vehicle Zephyr. It stands about 20 meters tall, has a diameter of 1.5 meters. It can place its payload at altitudes of 400 to 700 kilometres (the ISS orbits at 400 kilometres) and precisely position Smallsats in orbit without the need for their own propulsion. The first stage of the launch vehicle has seven Navier engines for velocity during the first 100 kilometres of altitude. The rocket then separates, and the second stage ignites with a single Navier engine designed for operation in a vacuum.
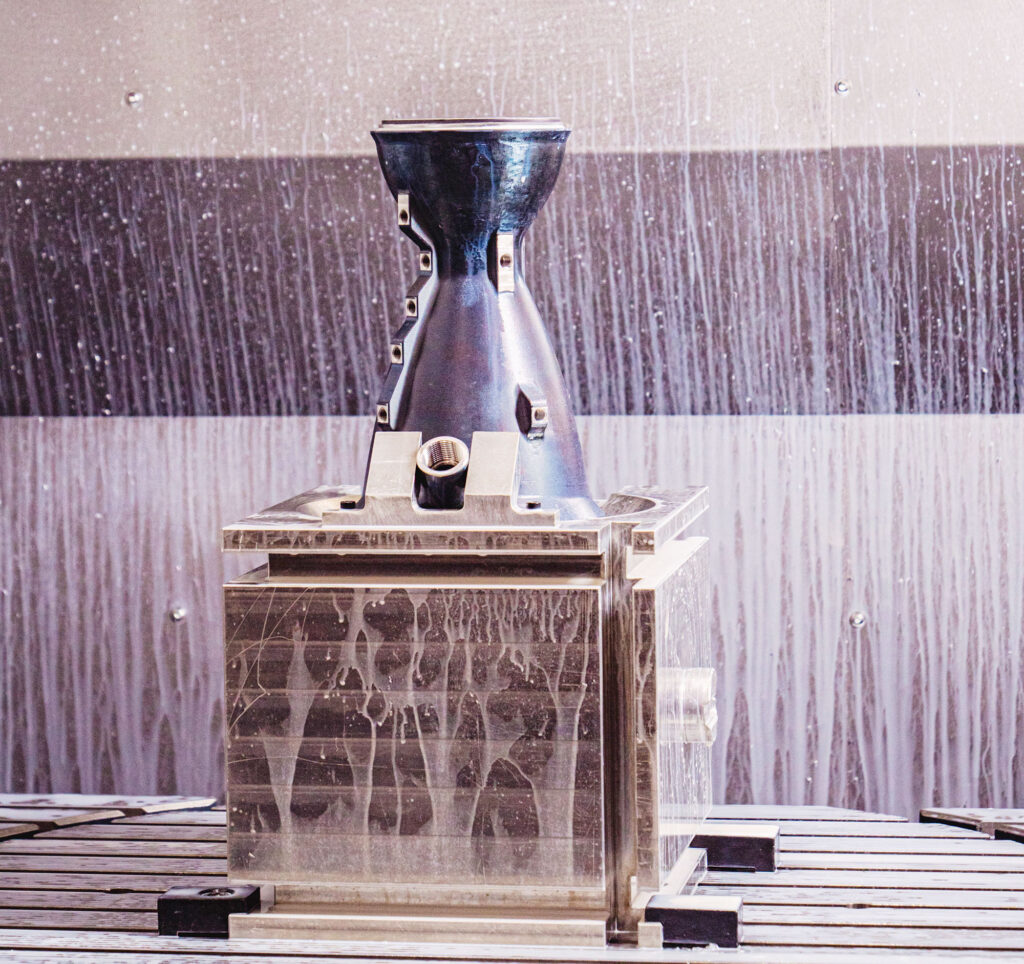
An attractive offer for the future market
The young French company aims to develop a powerful launch vehicle that is reliable and easy to use, providing an attractive offer to the market – above all to deploy many satellites into the exactly the right orbits in the shortest possible time. One of the first customers will be the French government. The French space agency CNES has booked the first flight with Latitude as part of a public tender.
Several important steps remain before the first commercial launch. The turbo pump, also an in-house development, is currently being tested. Its development and production will be completed in less than a year. The first flight of a Zephyr launch vehicle is planned for late 2025, with the first commercial flight expected in 2026.
Photos: Latitude